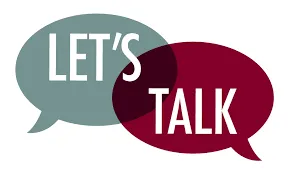
2021 domestic high-end machine tools set sail
1-1 Overview of machine tool industry chain and market
- the machine tool is the “industrial mother machine”, the industrial chain is clear
The technical level and product quality of the machine tool industry is important symbol to measure the development level of a country’s equipment manufacturing industry.
The whole machine tool industry chain is clear in the middle and lower reaches, including the upstream basic material and parts manufacturers, the mid-stream machine tool manufacturers, and the downstream end users.
Machine tools can be divided into 8 types based on the material shaping method: metal cutting machine tools, metal forming machines account for a higher proportion. Based on the selection/movement control mode, the machine tools include traditional machine tools and CNC high precision machine tools. Numerical control high precision machine tool refers to the machine tool that carries on high precision machining under the control of numerical control program control system.
-
- the global machine tool market pattern
- It has obvious periodicity and is still at the bottom of the cycle
Machine tools are characterized by periodicity. The general product life of machine tools is about 10 years, so the industry is about every 7-10 years for a business cycle. According to the statistical survey of the World Machine Tool industry published by Gardner Intelligence in the United States, the latest cycle began in 2008, and the global Machine Tool consumption and output value peaked in 2011 and then fell back, and the downward trend continued until 2016. In addition, according to the latest survey released by it, the market rebounded in 2017, but the global consumption of machine tools in 2019 was $82.1 billion, down 13.8% year on year, and the global industry is still at the bottom of the cycle.
- The demand of Asian countries is growing rapidly, and Germany and Japan are leading in technology
The world machine tool industry is a completely competitive industry, the main machine tool powers include China, Germany, Japan, the United States, and other countries. From the perspective of the region, the Asian market mainly contributed to the two rounds of industry growth in 2003-2008 and 2010-2011, among which the developing countries in Asia represented by China and India developed the most rapidly. China’s machine tool industry consumption and total output value as early as 2009 became the world’s first, until now China still maintains the world’s first machine tool production and consumption power status, every year to contribute one-quarter of the consumption and output value.
At present, the machine tool industry presents a pattern of high-end technology monopoly, the core technology is controlled in the hands of a specific country, a specific company, especially CNC machine tools, the key parts are mostly from Germany or Japan-related enterprises. The technology gap is reflected in stability, reliability, efficiency, precision, and other aspects. Germany attaches great importance to the high, fine, sharp, and practical CNC machine tools and accessories, and the research and development and production of various functional components are highly specialized, ranking the top in the world in quality and performance Japan focuses on the development of numerical control system, machine tool enterprises pay attention to the upstream material, component layout, integrated development of core products; The United States has strong competitiveness in CNC machine tool design, manufacturing, and basic scientific research.
2. “Past life and present life” of China’s machine tool industry
(a) Difficulties and hardships, in the beginning, rapid growth
China’s machine tool consumption and total output became the world’s largest in 2002 and 2009, respectively. Although the industry has been declining since the peak in 2011, China has remained the world’s largest machine tool producer and consumer until now. According to a statistical survey of the world machine tool industry conducted by Gardner Intelligence, the global machine tool consumption in 2019 is US $82.1 billion, of which China’s consumption is the US $22.3 billion, accounting for 27.2% of the global machine tool market. This is the first time since 2008 that China’s consumption of machine tools in the global machine tool consumption is less than 30%. In 2019, the global machine tool production scale reached the US $19.42 billion, accounting for 23.1% of the global market.
(b)” big but not strong”, domestic brands occupy the middle and low end of the market, high-end rely on imports
As the world’s largest machine tool producer, but the main competitiveness of domestic machine tool is concentrated in the low-end machine, if according to Mr. Sullivan, a consulting firm expression, in with 100,000 yuan of the flatbed CNC machine tools, 300,000 yuan of less than three-axis vertical machining center, such as 100,000 yuan in western mid-range machine tool market almost occupied more than 90% market share in the world. However, due to the late start of China’s machine tool industry, Chinese machine tool enterprises often rely on “quantity” to win in the industry competition, the added value of products is low, there is a large gap between the core technology and western manufacturing powers and Japan, and has not been able to gain an advantage in the world’s high-end machine tool market. As a result, China’s machine tool industry is in a serious trade deficit. According to Gardner Intelligence, in 2019, China’s trade deficit of import and export of machine tools was 2.87 billion yuan. Although it narrowed from more than 5 billion dollars in 2017 and 2018, it was still a large amount, with import accounting for 32.69% of consumption. Especially for the high-end machine tools represented by CNC machine tools, China imports more than 10000 units every year, and the import amount in 2019 is 2.9 billion US dollars.
There is a big gap between the import and export prices of metalworking machine tools. According to the statistics of the General Administration of Customs, the average import price of metalworking machine tools in recent years is between $100000 and $150000 per machine, in sharp contrast to the average export price of only $400-500 per machine.
The top 10 machine tool makers in 2019 are all from Germany, Japan, and the United States. At present, the number of domestic enterprises is large, but the general scale is relatively small, the market competitiveness is weak, the profitability is poor. According to the statistics of the National Bureau of Statistics, as of July 2020, the number of metal cutting machine tool enterprises in China is 817, the industry sales profit rate is only 3.99%. There are 526 metal-forming machine tool enterprises in China, and the profit rate of industry sales is 4.8%. From November 2015 to July 2020, the highest sales margins of the metal-cutting machine tool industry and the forming machine tool industry were only 5.49% and 7.88%.
(c)” Eighteen Arhat” fall, domestic machine tool industry ushered in structural adjustment
At the beginning of the construction of China’s industrial system, 18 state-owned machine tool factories have been developed. These 18 machine enterprises have made great contributions to the development of China’s machine tool industry. With the deepening of reform and opening up, most of these state-owned enterprises have carried out different forms of property rights system reform, and these state-owned enterprises have carried out different forms of property rights system reform, and these state-owned machine tool factories have also ushered in their own glorious moment. According to the “World Metal Processing Machine Ranks” released by Gardner Corporation in May 2012 in the Metalworking insiders Report, Shenyang Machine Tool Group’s output value in 2011 was $2.78 billion.
Due to the low entry threshold of the low-end market, competition intensifies. With the excess capacity of the low-end market, state-owned enterprises lose their vitality and gradually decline in this fully competitive market due to institutional reasons. Once “18 Ocean’s” have also experienced restructuring, bankruptcy, was acquired, currently only the second Ji’nan machine tool plant independent survival.
With the fall of state-owned enterprises, private enterprises are becoming the new main force of the machine tool industry, China’s machine tool industry into the structural adjustment. According to the China machine tool industry yearbook 2016, metal cutting machine tool enterprises above designated size in 2015 to 739, among them, the state-owned holding (group) holding, private and foreign investors (including Hong Kong, Macao, and Taiwan) number of companies holding 71533 and 105 respectively, the above three kinds of enterprises have assets accounted for 38.3%, 48.8%, and 10.4% respectively. Main business revenue accounted for 18.4%, 68.7%, and 10.8% respectively. The realized profits accounted for -12%, 97%, and 13.4% respectively. Private enterprises not only occupy the absolute advantage on the quantity but also contribute nearly 70% of the main business income and nearly 100% of the profit with less than half of assets. In recent years, a lot of competitive private enterprises have emerged, such as Shenzhen Genesis, YAWEI, Huadong Heavy Machinery (a subsidiary of Running Technology), Haitian Seiko, Rifa Precision Machinery, Guosengzhi, Neway CNC, and so on.
Three “timing, geographical, and people”, domestic high-end machine tools ushered in the development opportunity.
3.1 “Timeliness”: General equipment industry shows a recovery trend
Machine tools as general equipment, the whole industry has a strong pro-cyclical. Because machine tools and equipment are means of production capacity construction demands of the manufacturing industry. Therefore, its cycle logic is “profit improvement of downstream industrial enterprises—capacity investment expansion—equipment demand improvement”. First of all, profit recovery of downstream industry leads to more vigorous demand for capacity expansion, thus driving the growth of equipment investment.
On a macro level, the manufacturing PMI in August 2020 was 51.0, which has been above 50 for six consecutive months since the epidemic, maintaining the trend of recovery and strengthening. In addition, according to the logic of equipment investment, the profit index of industrial enterprises is the leading indicator of the prosperity of the general equipment industry. According to the observation data, the change of the total profit of industrial enterprises is basically consistent with the data of machine tool output and has certain precedence.
According to the data of new orders for machine tools published by the Japan Machine Tool Industry Association, the new orders in mainland China have continued to improve since entering the year 2020, with an increase of 1.848 billion yuan in July 2020, a year-on-year growth of 50.49%.
Industrial robot production speed up, side confirms the general equipment industry boom. Machine tools, lasers, injection molding machines, and industrial robots have different functions and utility, but they are all general equipment. Their downstream application fields are wide and highly overlapping, basically including the overall manufacturing industry and the development of several sub-industries shows strong consistency. Therefore, the performance of other industries can be seen from the side of the machine tool industry boom. The National Bureau of Statistics released the latest production data of industrial robots. In August 2020, the monthly output was 20663 units, up 32.5%year on year. The monthly growth rate was higher than that of 19.4% in July, and the monthly growth rate was still in a high state. In the first eight months, the accumulative production volume was 136873 units, up 13.9% year on year. The growth rate has maintained an upward momentum since it became positive in April.
According to the statistics of the National Organization Bureau, from January to July in 2020, the operating income of enterprises above the designated size in China’s machine tool industry decreased by 7.6% year-on-year, which was the same as that from January to June. Total realized profits fell 1.9% year on year, 0.6 percentage points are narrower than the January-June period. Main economic indicators of key associated enterprises of China Machine Tool and Tool Industry Association from January to July 2020 show that, after a severe decline in the first quarter and a continued recovery in the second quarter, July shows a new feature of rapid recovery. From the statistics, the overall operating income of the machine tool industry continues to narrow the decline, the total profit this year for the first time positive growth, metal processing machine tool new orders and orders in hand both increased.
3.2 “time”: high-end CNC machine tools downstream recovery and boom brought demand growth
(c)The division of middle and high-grade machine tools
The grade of the CNC machine tool is a relative and dynamic concept. At present, there is no unified
The authoritative definition of the classification standard of middle and high-grade CNC machine tools, which is formulated by the competent department, generally recognized by the industry and complied with by enterprises. According to the definition in the “Technology Roadmap for Key Fields (2015 Edition)” of Made in China 2025, high-grade CNC machine tools refer to CNC machine tools with high-speed, precision, intelligence, composite, multi-axis linkage, network communication, and other functions. According to “High-grade CNC Machine Tools and Robots” (Yang Zhengze, Li Xiangdong), the CNC machine tools using semi-closed-loop DC servo system and AC servo system are divided into middle and high-grade. The 2-4 axis or 3-5 axis above the CNC machine tools are classified as high-grade. Will have communication and networking functions of CNC machine tools are classified as high-grade. The CNC machine tools with three-dimensional graphics display functions are classified as high-grade.
At present, China's machine tool industry "difference" in the middle of the planning work is steady progress, for during the period of "difference" that represented by high-grade CNC machine tool machine tools and equipment series product international competitiveness has improved significantly, solve a number of high-grade CNC machine tool numerical control system, the key functional components manufacturing the time "problem, research and development of a number of key areas in urgent need of machine tools and equipment.